Morris Minor with Grandad
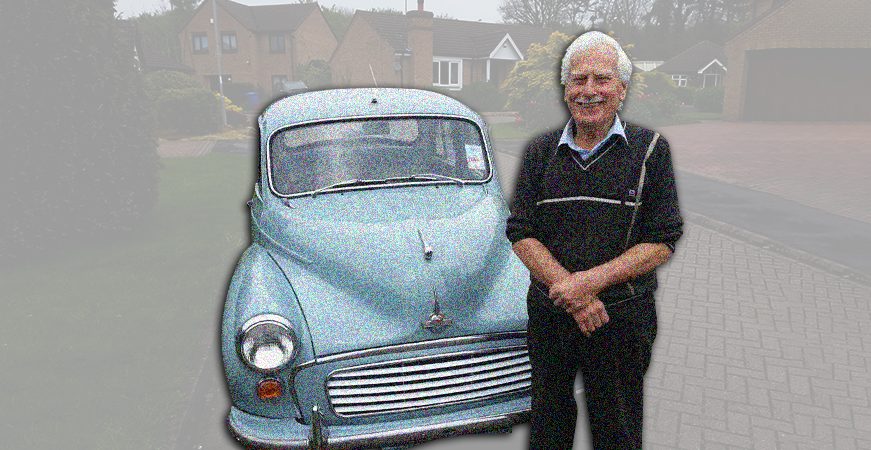
Having restored a number of Mini’s and in his early retirement and generally being regarded as a bit of a genius with all things mechanical, I have always wanted to be a little bit (OK, a lot!) more like my Grandad that is when I got the idea for us to restore a Morris Minor.
Over tea (and Scottish shortbread of course!) one day, I found myself hearing him say “I’m thinking of dusting off the spanners and getting a bit of a project.” I can only assume after years of tinkering with old cars he had become despondent with mowing the lawn and attending his vegetable patch. As enthusiastic as ever about the chance of saving an old car and spending some time in the garage together, I found myself making the statement “I’ve always wanted to weld!” For obvious safety reasons it was the one garage activity I had never fully witnessed as a youngster, often banished from the building whilst he fired up the welder! Only to watch from the outside as the garage mystically illuminated, followed by the fizzing and crackling sound I now know so well.
Before the week had passed I received a rather excited phone call from my Grandad, informing me of our recent purchase! Having received a crash course in the dark arts of the internet and roping in my stepdad Phil to help, my Grandad had ensured we were now the proud owners of a 1962 project Morris Minor 1000. A week later as arranged, I arrived to see what exactly we had let ourselves in for. I think it is safe to say it dawned on me that my statement about wanting to learn to weld had certainly had an influence on my Grandad’s criteria and buying motive’s for our project!
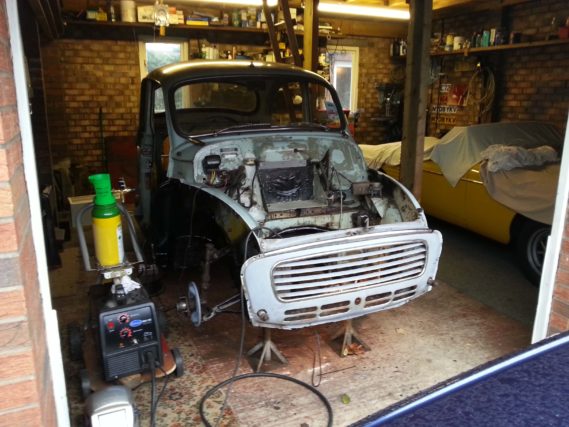
Embarking on the initial strip down of our “Moggy”, I believe it began to be apparent the size of the project we had excitedly landed ourselves with. Having said this, I now know neither of us wanted to admit it. (At least not to each other!!) We will order some steel, a few panels and some gas for the welder shouted my Grandad. Think of it as a class room exercise he said somberly. If nothing else, we will practice on her, get you welding and then scrap her as she is far too gone for our level of skill and inexperience. Having excitedly ordered the materials and found Hobbyweld, who would supply and deliver to our door a cylinder of Hobbyweld 5, I set about my welding training under my Grandad’s expert tuition. To my surprise, I took to the welding and really enjoyed it. More than I expected to actually. I wont lie, there were days when the air was blue in the garage. (And that was with the welder turned off!) Knuckles were skinned, fingers burnt on hot metal and days when we seemed to go backwards.
Even more to our surprise, the Moggy was really starting to take shape. Most of the floor replaced, rotten chassis rails cut out and new fresh metal welded back in its place. Engine and gearbox were soon back in. With all the fingers we had crossed and a quick glance to the heavens we fired the old Moggy up. She lives!
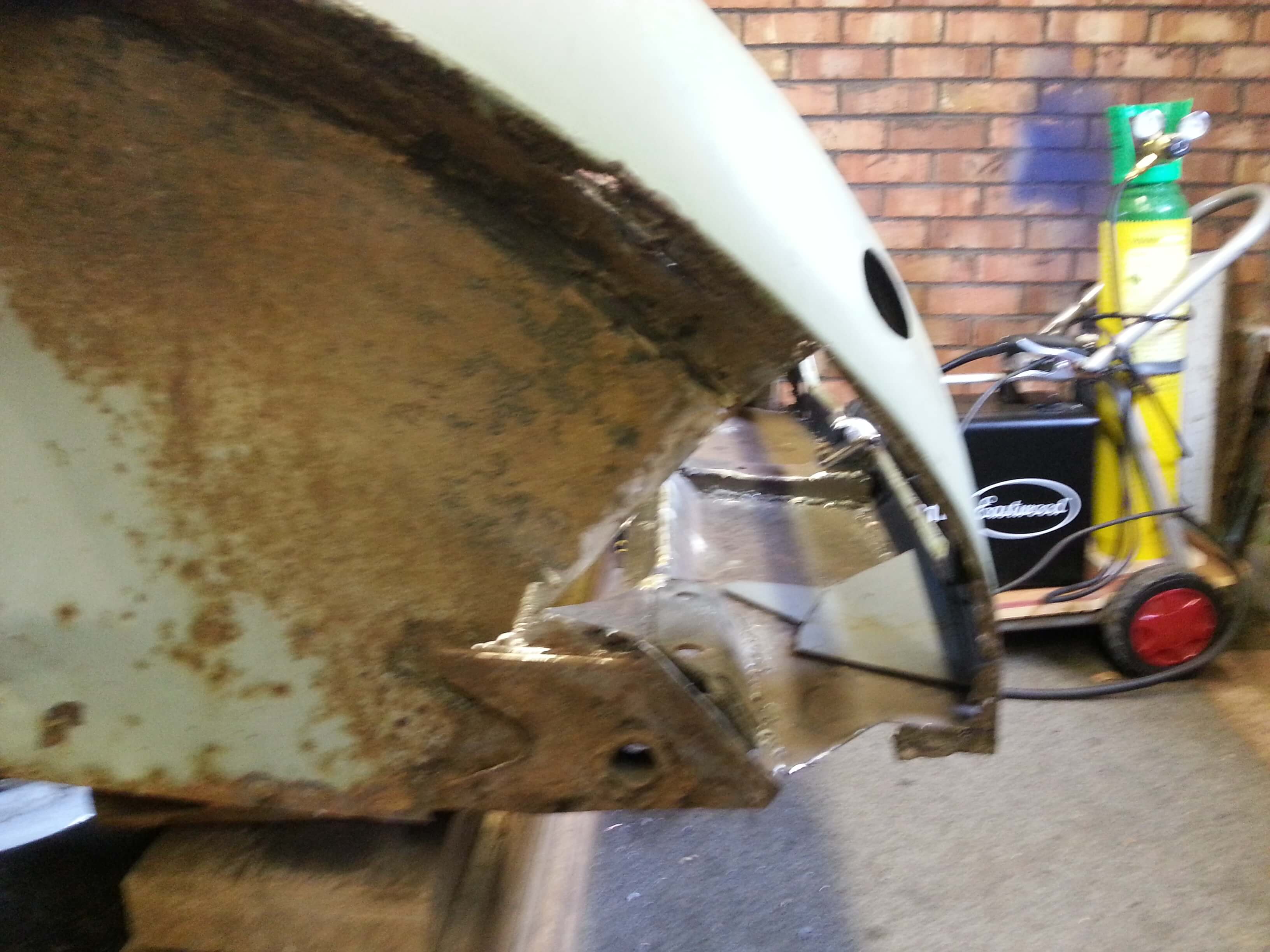
In the last few weeks we have patched up some of the untidy bodywork and used my new found welding skills to an effect neither of us would have believed possible 6 months ago. The wings and body panels are back on. Happily the doors fit and work beautifully. You really wouldn’t believe it was the same Morris Minor as the one we began with if it wasn’t for the photos we had taken for pleasure and a memento of our time spent. (Now doubling up as evidence, proof of our efforts along the way!)
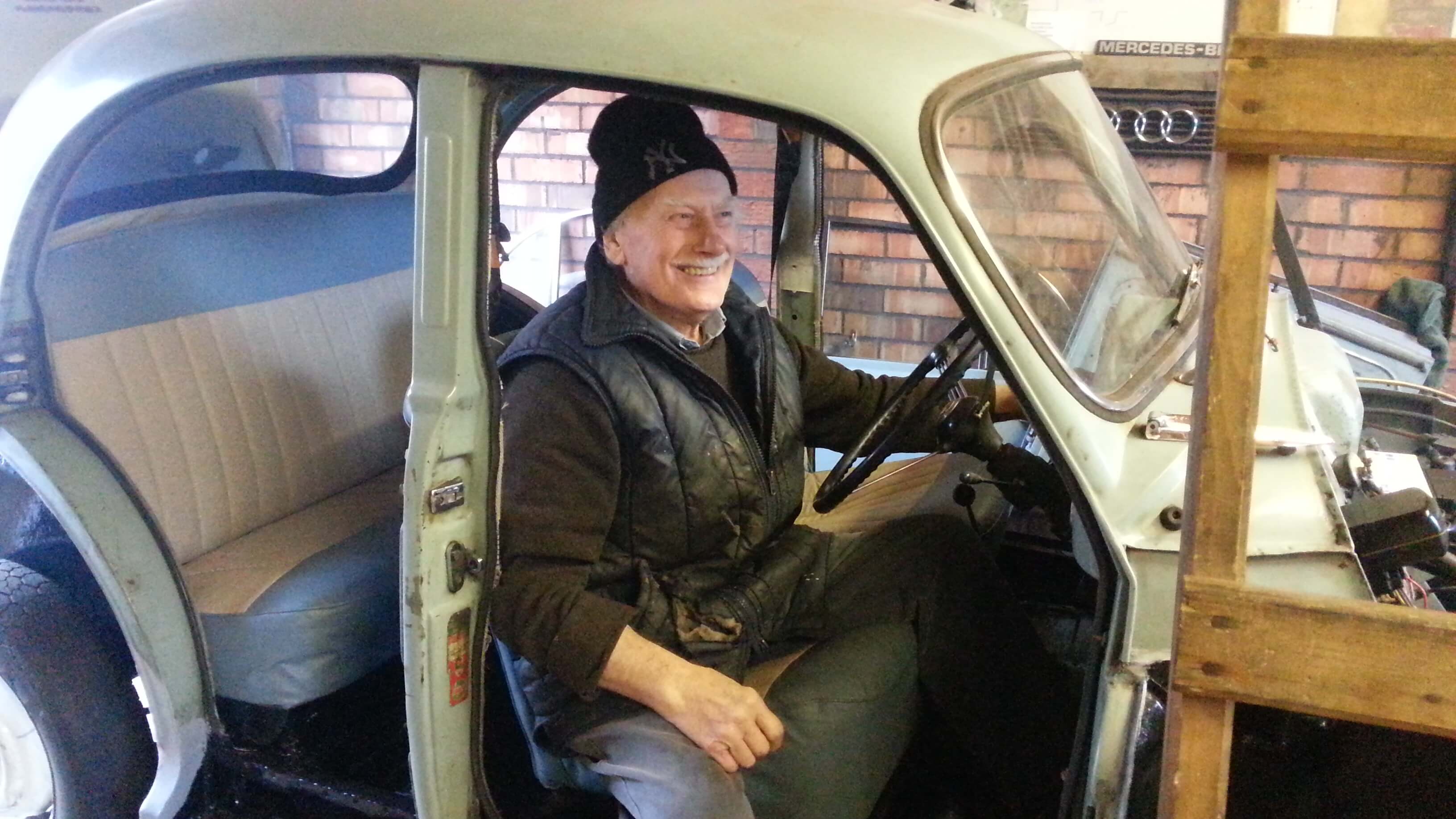
I hope you enjoy some of these photos and this story of our journey.
In this day and age, not many people take time out to say thank you for a job well done. Being a bit old fashioned (Again my Grandad’s influence!) I would like to extend heartfelt thanks to Hobbyweld. To all of the team there for great help, advice and a personal service, all of which are often lost in these busy times. Especially to Sue and John who are a credit to your organisation and a pleasure for your customers to deal with……. Thank you.
Here’s to home hobbyists, time spent with loved ones passing on knowledge and to the suppliers who make this possible.
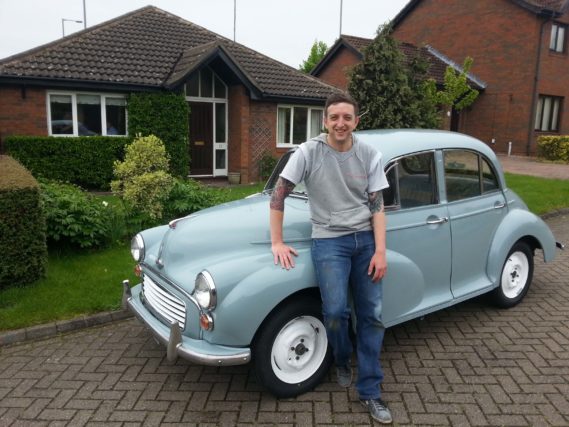
Article by John Holmes | Visuals provided by Dean Masterson